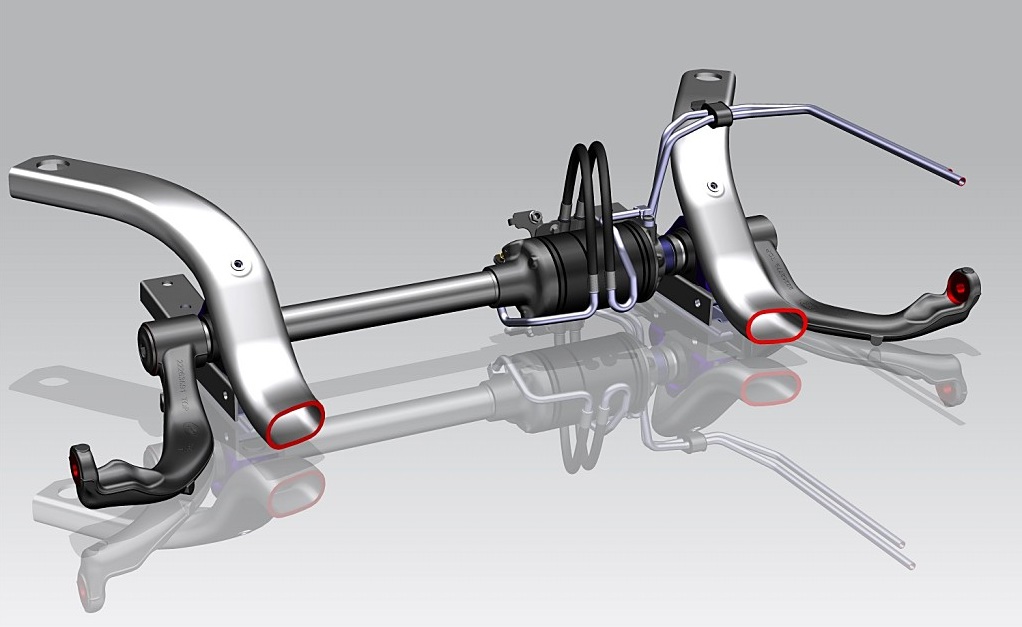
Active Stabilization / Dynamic Response System Land Rover : maintains the attitude of the vehicle body when cornering. The system is both electrically and hydraulically
Range Rover – Active Stabilization / Dynamic Response System
DYNAMIC RESPONSE
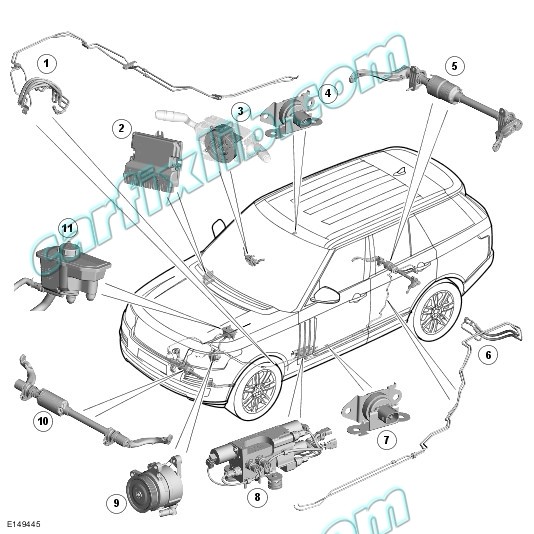
ITEM | DESCRIPTION |
---|---|
1 | Hydraulic pipes forward of dynamic response valve block |
2 | Dynamic response control module |
3 | Steering wheel angle sensor |
4 | Accelerometer – upper |
5 | Stabilizer bar and dynamic response actuator – rear |
6 | Hydraulic pipes reward of dynamic response valve block |
7 | Accelerometer – lower |
8 | Dynamic response valve block |
9 | Dynamic response hydraulic pump |
10 | Stabilizer bar and dynamic response actuator – front |
11 | Dynamic response fluid reservoir |
OVERVIEW
In operation the two-channel Dynamic Response System maintains the attitude of the vehicle body when cornering. The system is both electrically and hydraulically operated and controlled by the Dynamic Response Control Module located on the driver’s side ‘A’ post, behind the instrument panel.
The Dynamic Response System uses a two-channel operation to independently control the front and rear axles. This system transforms vehicle handling and occupant comfort by dramatically reducing the amount of body lean during cornering.
The latest two channel technology has allowed the system to be tuned to deliver increased low-speed agility, along with enhanced control and stability at speed.
A new comfort mode feature improves ride comfort at low speed by detecting and eliminating the body rock induced by uneven road surfaces.
If the system detects off-road conditions, the control module also reduces the level of roll compensation, to allow greater wheel articulation therefore increasing the contact with the terrain and improving comfort. This is done as a function of road roughness and vehicle speed.
The following illustrations demonstrate the difference in body angle between a vehicle fitted with conventional ‘passive’ stabilizer bars and a vehicle fitted with the Dynamic Response System.
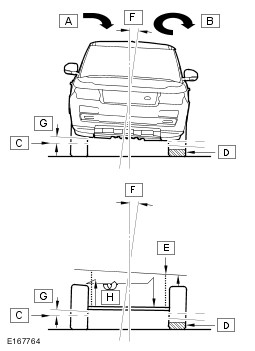
ITEM | DESCRIPTION |
---|---|
A | Direction of travel – Right hand bend |
B | Direction of travel – Right hand bend |
C | Axle roll |
D | Tire squash |
E | Dampers |
F | Body roll angle |
G | Drive line roll angle |
H | Direction of stabilizer bar twist |
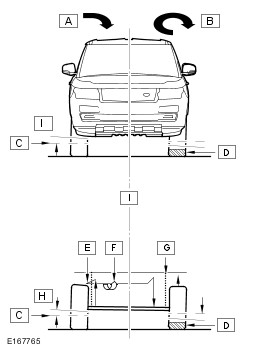
ITEM | DESCRIPTION |
---|---|
A | Direction of travel – Right hand bend |
B | Body roll |
C | Axle roll |
D | Tire squash |
E | Stabilizer bar |
F | Direction of stabilizer bar twist |
G | Dampers |
H | Drive line roll angle |
I | Reduced body roll with Dynamic Response System |
With the same cornering forces applied a ‘passive’ system will have a greater roll-angle than a vehicle fitted with a Dynamic Response System. The Dynamic Response System allows minimal roll up to 0.4g then progressive roll thereafter.
The Dynamic Response System is also able to modify the handling balance of the vehicle, that is the understeer/oversteer characteristics, by applying a different pressure to both the front and rear stabilizer bar actuators. This provides a more agile vehicle at lower speeds, while providing a more composed feel at high speed.
The system also acts to reduce roll accelerations due to uneven road surfaces. The Dynamic Response System can detect when the vehicle is being driven off-road and if the vehicle is travelling at 25 mph (40 km/h) or less. In these circumstances the Dynamic Response Control Module will reduce the roll compensation. In circumstances when driving on side-slopes of more than 11 degrees the Dynamic Response System will switch to a ‘locked bars’ condition at slow speed. The ‘locked bars’ condition will allow the stabilizer bars to operate in a similar manner as conventional ‘passive’ stabilizer bars.
DESCRIPTION
Fluid Reservoir and Filter
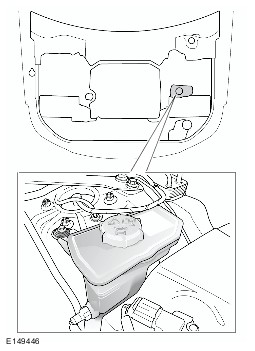
The fluid reservoir and system filter is located in the front left hand side of the engine compartment. The reservoir is attached to the suspension tower.
The reservoir is a molded plastic container with a breathable cap.
Two connections on the bottom of the reservoir provide for connection of the feed pipe to the pump and the return pipe from the valve block.
The reservoir contains the main filter for the system which acts on the fluid returning from the valve block; a coarse nylon-mesh filter removes particulate matter from the fluid before it is drawn into the pump. The filter/reservoir assembly must be changed at the intervals defined on the vehicle service schedule and if a system hydraulic component is replaced.
Upper and lower fluid level marks are molded onto the reservoir body.
Dynamic Response Hydraulic Pump
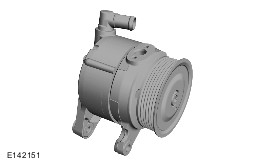
The Dynamic Response Hydraulic Pump is located on the left hand side of the engine. The pump is attached to a mounting bracket above the air conditioning compressor. The pump is driven by the auxiliary drive belt from the crankshaft.
The engine driven hydraulic pump supplies a constant hydraulic flow to the valve block.
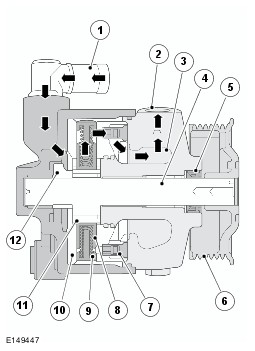
ITEM | DESCRIPTION |
---|---|
1 | Inlet port |
2 | Outlet port |
3 | Silencer volume |
4 | Shaft |
5 | Shaft seal |
6 | Pulley |
7 | Discharge valve |
8 | Piston |
9 | Piston spring |
10 | Cylinder housing |
11 | Cam ring |
12 | Counter balance |
The hydraulic pump is driven at approximately 1.7 times crankshaft speed by the auxiliary drive belt.
The pump is a radial piston type which can deliver an almost constant flow rate of fluid across the engine speed-range.
It has eight pistons located in bores in a cylinder block. A balanced central shaft which has an eccentric cam operates the pistons as the shaft rotates, the shaft driven by a balanced pulley.
The cam acts against each piston in turn, and pushes it outward, moving the fluid above the piston. The pressure created by the fluid flow from the bore opens a spring loaded discharge valve. When the valve opens, the pressurized fluid flows, via the silencer volume area of the pump housing, to the outlet port. The silencer volume assists with damping out operating noise from the pump. When the piston reaches its full stroke, the flow reduces and the discharge valve closes under spring pressure.
As the cam moves away from the piston, a spring pushes the piston down the bore, creating a vacuum above the piston. As the piston moves down the bore, ports in the piston are exposed and connect with the fluid inlet port. The vacuum draws fluid into the piston filling the piston and the chamber above it. As the piston is again pushed upwards, the ports in the piston are closed off by the bore and the pressurized fluid opens the discharge valve and flows to the outlet port.
The above sequence is applied to each of the eight pistons for every revolution of the shaft and cam. When the engine is running the sequence occurs rapidly creating a constant flow of fluid. The fluid flow varies with engine speed and the rotational speed of the shaft up to its maximum value at 1000rpm. The pressure applied to the actuators, created by the flow from the pump, is controlled by the valves in the valve block.
The pump has a displacement of 6cm3/rev and an operational pressure of 180 bar (2610 lbf/in2). The pump output flow ranges from 6.5 l/min (1.7 US Gallons/min) at idle to 10 l/min (2.64 US Gallons/min) at 1000 rev/min and above.
Dynamic Response Valve Block
Stabilizer Bars and Dynamic Response Actuators
System Pipes
Fluid is moved through the Dynamic Response System via a series of six pipes and hoses. The pipes are mounted on brackets at strategic points to provide quiet operation of the system.
The pipes connecting the pump, reservoir and actuators are one-piece components. If the pipes require replacement during service, the pipes are supplied as either a front or rear bundle. Actuator pipes can be split at the tube nut to aid removal.
The flexible hose which supplies pressure from the pump to the high pressure pipe is fitted with attenuators. The attenuators comprise of tuned lengths of PTFE pipe and restrictors within the flexible hose. The attenuators damp pressure pulsations in the hydraulic fluid produced by the pump, reducing noise and strain on components downstream. The attenuator is integral with the high pressure hose and cannot be serviced separately.
A cooler is fitted in the primary circuit to maintain fluid temperature within an acceptable working range.
Dynamic Response Control Module
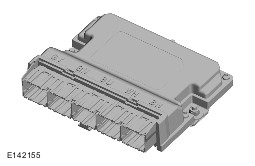
The Dynamic Response Control Module is located on the driver’s side ‘A’ post, below the instrument panel. The Dynamic Response Control Module is secured to a bracket with three nuts. Three connectors are located on the lower face of the Dynamic Response Control Module and allow for the connection of the harness connectors. The three connectors supply power, ground, signal and sensor information to and from the Dynamic Response Control Module for control of the Dynamic Response System.
Accelerometers
Two accelerometers are used, an upper and a lower. Both accelerometers are identical in their construction. The lower accelerometer is secured to the underside of the vehicle floor, on the left hand inner sill panel, below the front door. The upper accelerometer is secured to a bracket on the body roof panel, in a central position at the top of the windscreen.
The lower accelerometer is the primary sensor used to measure lateral acceleration of the vehicle for roll control. The upper accelerometer is used by the Dynamic Response Control Module for roll correction and fault detection in conjunction with the lower accelerometer.
The lower accelerometer is the primary sensor used to measure lateral acceleration of the vehicle for roll control. The upper accelerometer is used by the Dynamic Response Control Module for roll correction and fault detection in conjunction with the lower accelerometer.
Each accelerometer is a capacitive acceleration sensor and operates on a 5 volt supply from the Dynamic Response Control Module. The upper and lower accelerometers can measure acceleration in the range of ±1.11 g and return an output to the Dynamic Response Control Module of between 0.5 and 4.5 volt. Failures of an accelerometer are recorded by the Dynamic Response Control Module and can be retrieved using Land Rover approved diagnostic equipment.
OPERATION
The Dynamic Response Control Module receives a power supply from the main relay in the EJB (engine junction box).
Vehicle lateral acceleration is sensed by two accelerometers. Signals from these together with the steering angle sensor and vehicle speed are transmitted to the Dynamic Response Control Module.
An engine speed signal is transmitted to the Dynamic Response Control Module from the ECM (engine control module) via the high-speed CAN (controller area network) powertrain bus. The engine speed signal is used by the Dynamic Response Control Module to detect that the engine is running and hydraulic pressure for the Dynamic Response System is available.
A road speed signal is transmitted to the Dynamic Response Control Module from the ABS (anti-lock brake system) module on the high-speed CAN (controller area network) powertrain bus. A steering-angle signal is transmitted on the high-speed CAN (controller area network) chassis bus from the steering angle sensor. The Dynamic Response Control Module uses the steering angle signal to improve system response and uses steering angle and road speed signals to calculate lateral movement.
When reverse gear is selected and reverse wheel-rotation is transmitted on the high-speed CAN (controller area network) powertrain bus, the Dynamic Response System reverts to a ‘locked bars’ condition by closing the Safety Control Valve. This condition is maintained until reverse gear is deselected and a forward wheel-rotation message is transmitted on the CAN (controller area network) bus.
The Dynamic Response Control Module receives an ignition on signal on the high-speed CAN (controller area network) powertrain bus. The ignition signal provides an input into the Dynamic Response Control Module to inform the control module that the ignition is on. The control module initiates a 250 millisecond start time which is used to prevent functions operating when the software routines are being initialized.
When the “ignition on” CAN signal is removed, the Dynamic Response Control Module senses that the ignition has been switched off. The control module remains powered for a 60 second period to allow fault information and adaptive values to be stored in the memory.
The values and fault information are read by the control module when the ignition is next switched on. The module is permanently powered by a direct feed from the fuse box and operation is controlled by a hardwired ignition signal. The Dynamic Response control module is connected on the high-speed CAN (controller area network) powertrain bus to the diagnostic socket which allows diagnostic interrogation of the control module. The diagnostic socket allows for the connection of a Land Rover approved diagnostic equipment to read any stored fault codes in the control module. The control module can also be updated with revised software should a software update be required. As stated in this article, you can browse your selection of available deals on smartphones and top brands and explore the service plans that best suit your needs.
The Dynamic Response control module supplies a control current to the Pressure Control Valve and Proportional Direction Control Valves in the valve block. The currents supplied are determined by a number of input signals from the upper and lower accelerometers, road speed, steering angle etc. The Proportional Directional Control Valves controls the hydraulic pressure supplied to the actuators proportional to the current supplied by the control module, to a level determined by the calibration in the control module.
The Dynamic Response control module supplies a current to the Safety Valve to hold it open during normal operation when the vehicle is moving.
The pressure transducer located in the valve block receives a 5 volt current from the control module. The transducer measures the hydraulic pressures in the range of 0 to 200 bar (0 to 2900 lbf/in2) and returns a linear output voltage to the control module dependent on the hydraulic pressure.
The Dynamic Response control module supplies a 5 volt current to each of the accelerometers. Each accelerometer is capable of measuring lateral acceleration in the range of ± 1.11 g. An analogue input to the control module of between 0.5 and 4.5 volt relative to the lateral acceleration sensed is returned by each accelerometer. The control module processes the two signals received, together with the steering angle and vehicle speed signals, to produce a ‘pure’ lateral acceleration signal which is then used as the main control signal for the Dynamic Response System.
When system faults are detected, the control module issues a message on the CAN bus which is received by the instrument cluster. The instrument cluster then illuminates Dynamic Response warning indicator as follows:
- Minor faults – warning indicator illuminated in an amber color with an applicable message in the message center.
- Major faults – warning indicator illuminated in a flashing red color with an applicable message in the message center and an audible warning.
The message will instruct the driver to stop the vehicle immediately or drive with caution. Two messages relating to Dynamic Response are displayed in the instrument cluster message center:
- SUSPENSION FAULT, VEHICLE LEAN, WHEN CORNERING.
- SUSPENSION FAULT, STOP SAFELY, STOP ENGINE.
Failure Modes
HYDRAULICS
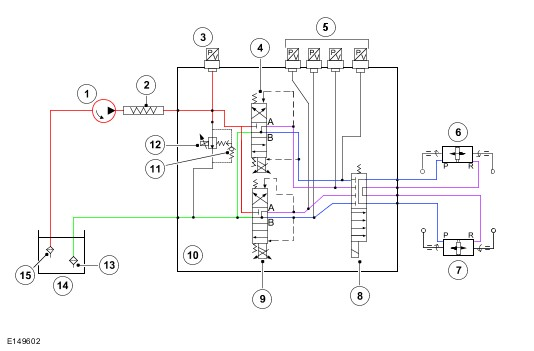
ITEM | DESCRIPTION |
---|---|
1 | Dynamic response hydraulic pump |
2 | High-pressure attenuator |
3 | Pressure control valve, pressure sensor |
4 | Proportional Directional Control Valve – front |
5 | Actuator feed pressure sensors |
6 | Front actuator |
7 | Rear actuator |
8 | Safety valve |
9 | Proportional Directional Control Valve – rear |
10 | Valve block |
11 | Pressure relief valve |
12 | Pressure control valve |
13 | Return filter |
14 | Reservoir |
15 | Suction filter |
Vehicle Not Moving
When the engine is running and the vehicle is not moving, the Safety Valve is closed, locking fluid in each side of the actuator piston. The hydraulic pump draws fluid from the reservoir and passes it at low pressure to the valve block.
Because the Safety Valve is closed, the fluid it is directed through the Pressure Control Valve to the reservoir.
The Pressure Control Valve is open fully to allow the full flow to pass to the reservoir without an increase in system pressure. The Safety Valve will remain closed until the control module detects a requirement to operate.
Vehicle Moving and Turning Left
When the vehicle is turning left, the steering sensor detects steering angle and the accelerometers detect the cornering forces applied. These signals are transmitted to the control module. The control module determines that an opposing force must be applied to the stabilizer bars to counter the cornering forces. The control module supplies a current to the correct coil of the front and rear Proportional Directional Control Valves. Simultaneously, a current is supplied from the control module to the Pressure Control Valve which operates to restrict the flow of fluid returning to the reservoir.
The restriction causes the hydraulic pressure in the system to rise and the pressure is sensed by the pressure transducers which send a signal to the control module. The control module determines from the inputs it receives what pressures are required and adjusts the pressures accordingly.
The pressures in the system are applied to the piston of each actuator, applying a force to the stabilizer bar and minimizing the cornering effect on the vehicle and maintaining the vehicle attitude. The fluid displaced from the other side of the piston is returned to the reservoir via the valve block.
As the cornering force is removed when the vehicle straightens up, the control module modulates the Proportional Directional Control Valves and opens the Pressure Control Valve to reduce the pressure in the system. The fluid bleeds from the actuator back into the system as the cornering force is reduced, removing the force applied to the stabilizer bar.
Vehicle Moving and Turning Right
When the vehicle is turning right, the steering sensor detects steering angle and the accelerometers detect the cornering forces applied. These signals are transmitted to the control module. The control module determines that an opposing force must be applied to the stabilizer bars to counter the cornering forces. The control module supplies a current to the correct coil of the front and rear Proportional Directional Control Valves. Simultaneously, a current is supplied from the control module to the Pressure Control Valve which operates to restrict the flow of fluid returning to the reservoir.
The restriction causes the hydraulic pressure in the system to rise and the pressure is sensed by the pressure transducers which send a signal to the control module. The control module determines from the inputs it receives what pressures are required and adjusts the pressures accordingly.
The pressures in the system are applied to the piston of each actuator, applying a force to the stabilizer bar and minimizing the cornering effect on the vehicle and maintaining the vehicle attitude. The fluid displaced from the other side of the piston is returned to the reservoir via the valve block.
As the cornering force is removed when the vehicle straightens up, the control module modulates the Proportional Directional Control Valves and opens the Pressure Control Valve to reduce the pressure in the system. The fluid bleeds from the actuator back into the system as the cornering force is reduced, removing the force applied to the stabilizer bar.
Vehicle Moving in a Straight Line
The control module is constantly monitoring the signals received and operates the Proportional Directional Control Valves and Pressure Control Valve to maintain the vehicle attitude when the vehicle is moving. When the vehicle comes to rest the Safety Valve will remain open for 15 seconds to allow for any air suspension leveling operations to be performed prior to closure.
Off-Road Driving
Off-road detection is achieved by the control module by monitoring the signals from the upper and lower accelerometers for varying degrees of body movement. Off-road driving generates differing signals to the accelerometers which in turn produce differing outputs due to their vertical separation and the location of the roll center of the vehicle.
The two signals are passed through a filter to remove any offset caused by the vehicle leaning or the terrain. The control module then uses this signal to calculate the percentage of road roughness.
Below 25 mph (40 km/h) the percentage of road roughness calculated is used by the control module to limit the operation of the Dynamic Response System. At speeds above 25 mph (40 km/h) the system disables the percentage road roughness signal and full Dynamic Response System assistance is restored. The system is completely inoperative at speeds below 2 mph (3 km/h).
Side Slope Detection
The control module uses side slope detection when the upper and lower accelerometers detect an average acceleration of more than ± 0.2 g or 11 degrees of side slope and a road speed of less than 25 mph (40 km/h).
When side slope is detected, the Safety Valve is closed to provide a ‘locked bars’ condition. This condition increases stability and gives a constant vehicle response. As the road speed increases up to 25 mph (40 km/h), the level of average lateral acceleration must also increase and be maintained for the system to recognize that the vehicle is on a side slope. If the side slope angle is steep and the road speed is low, the control module will detect the side slope in a short time.
CONTROL DIAGRAM
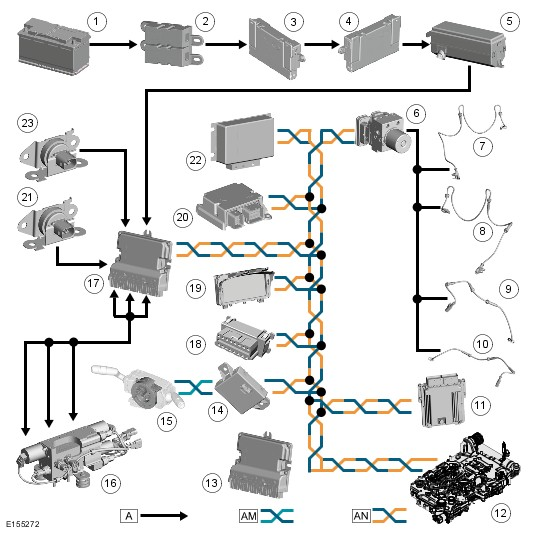
ITEM | DESCRIPTION |
---|---|
A = Hardwired; AM = High Speed CAN (controller area network) Chassis bus; AN = High Speed CAN (controller area network) Powertrain bus | |
1 | Battery |
2 | Battery junction box- 2 |
3 | Battery junction box |
4 | Auxiliary junction box |
5 | Engine junction box |
6 | ABS module |
7 | Wheel speed sensor |
8 | Wheel speed sensor |
9 | Wheel speed sensor |
10 | Wheel speed sensor |
11 | Engine control module |
12 | Transmission control module |
13 | Integrated suspension control module |
14 | Gateway module |
15 | Steering angle sensor integrated with clockspring |
16 | Dynamic response valve block |
17 | Dynamic response control module |
18 | Diagnostic socket |
19 | Instrument cluster |
20 | Restraints control module (incorporating the yaw rate lateral acceleration sensor) |
21 | Accelerometer – lower |
22 | Transfer case control module |
23 | Accelerometer – upper |
Was this helpful?
1 / 0