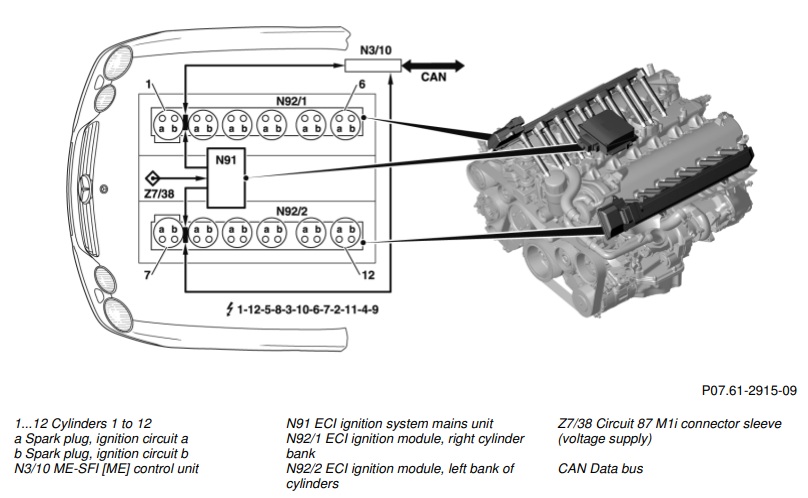
Mercedes, MAYBACH – ECI Ignition System ENGINE 275, 285
Ignition ENGINE 285.950 in MODEL 240 MAYBACH
Ignition ENGINE 285.980 in MODEL 240 MAYBACH
Ignition ENGINE 275.950 in MODEL 215, 220 Mercedes
Ignition ENGINE 275.951 in MODEL 230 Mercedes
Ignition ENGINE 275.953 in MODEL 216, 221 Mercedes
Ignition ENGINE 275.954 in MODEL 230 Mercedes
Ignition ENGINE 275.980 in MODEL 215, 220 Mercedes
Ignition ENGINE 275.981 in MODEL 230 Mercedes
Ignition ENGINE 275.982 in MODEL 216, 221 Mercedes
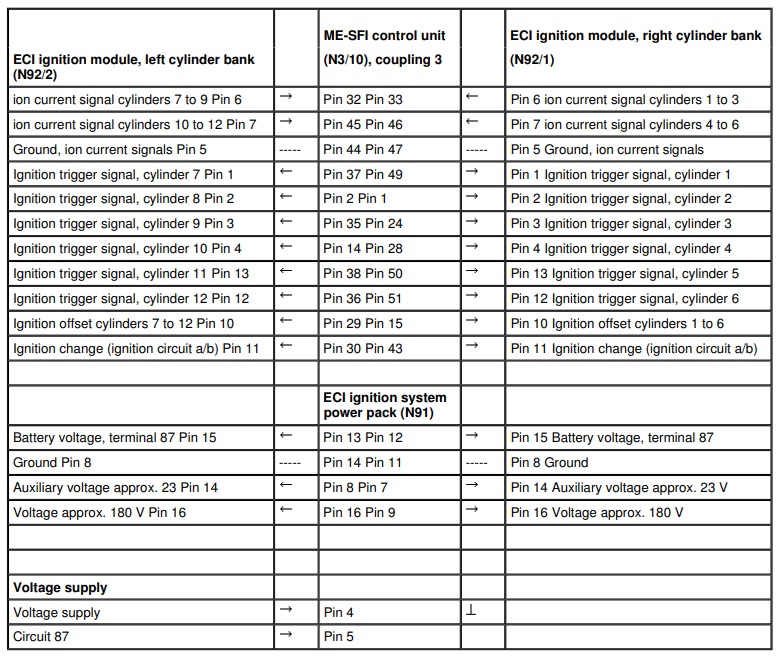
The short name for the AC ignition system ECI means:
E = Energy (energy)
C = Controlled (controlled)
I = Ignition (ignition system)
The ignition system ECI must initiate combustion by creating a spark at the spark plugs. This requires an adequately high voltage for generating a spark at the end of the spark plug and the sparks must also have sufficient energy to ensure guaranteed combustion of the fuel / air mixture.
The ignition system must be insensible to carbon fouled spark plugs and guarantee a high spark plug working life.
The ignition system ECI consists of:
- The ignition module ECI for the right cylinder bank
- The ignition module ECI for the left cylinder bank
- ECI ignition system mains unit
- Evaluation circuit for the ion current in the ME control unit
- Actuation of the ignition system ECI by the ME control unit
- Actuation of the ignition system ECI by the ME control unit
- Ignition map in the ME control unit.
No spark tests can be undertaken with the ignition system ECI.
The ignition system ECI has the following sub-functions:
- Generation of the ignition voltage (ac voltage).
- There is an output stage for each spark plug in the ignition modules. The ignition coils
are arranged in the spark plug connectors. The output stages with oscillating circuit
generate the ignition voltage from an input of about 180 V. - The ME control unit produces the following actuation impulses:
- Triggering of the ignition spark according to the ignition angle
- Permanent control of the ignition process
- Change of ignition
- Ignition offset
- There is an output stage for each spark plug in the ignition modules. The ignition coils
- Measurement of the ion current : There is a switchover to ion current measurement at the end of the ignition spark phase and the ion current on the spark plug is measured with the help of an auxiliary voltage of about 23 V. Evaluation of the ion current signals takes place in the ME control unit. The signals are used for detection of combustion misfires at high rpms.
- The power pack generates the required voltages of two times about 180 volts and two times about 23 volts.
Generation of the ignition voltage (ac voltage)
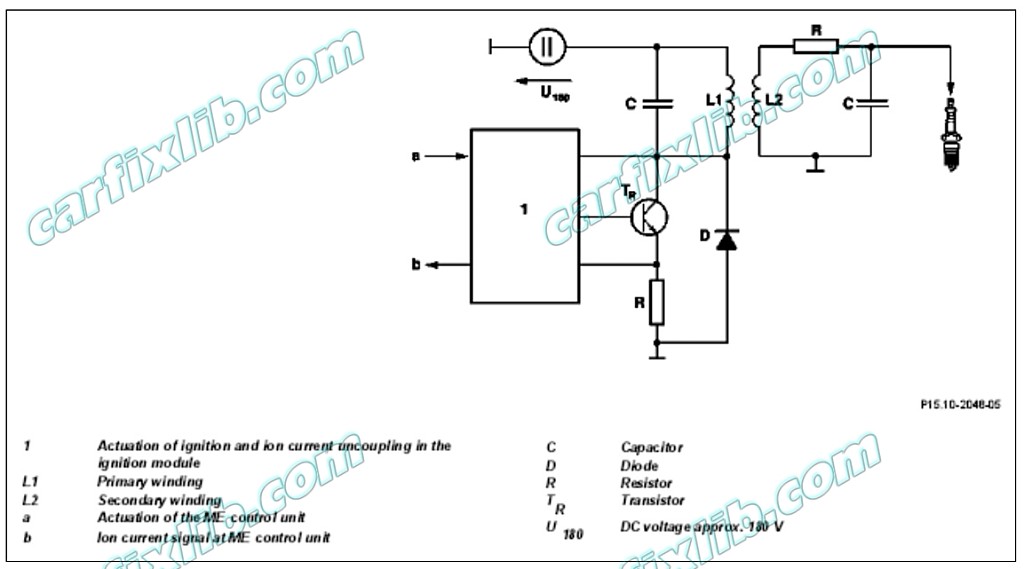
The ignition voltage is generated in two steps:
- Transistor (T ) closed – the voltage U is transferred to the R secondary side.
- Transistor (T ) opened – the negative half wave of the AC voltage develops and is also transferred to the secondary side.
Control of the transistor can theoretically allow generation of an AC voltage of any desired duration and energy level.
The maximum spark burning period is, however, limited by the rated output of the power pack ECI of two times 55 watts depending on the engine speed to about 0.15 to 1.5 msecs. A spark burning period of about 0.1 msecs is usually quite adequate for guaranteed combustion of the fuel / air mixture.
The rapid increase in ignition voltage makes the ignition system ECI insensible to carbon fouled
spark plugs e.g. due to frequent cold starts.
Permanent control of the ignition process
Adjustment of the spark energy over the spark duration to the actually required ignition energy of the fuel / air mixture occurs controlled by the ME control unit according to the performance map.
The spark plugs enjoy 4 times their usual working life due to spark duration control. Combining this at the same time with the use of spark plugs with platinum electrodes allows the working life to be extended even further.
Ignition offset and ignition change
In the lower part load range up to approx. 2000 rpm both ignition sparks of a cylinder are triggered simultaneously. At moderate and high engine loads, the ignition sparks are triggered offset by as much as 10° crank angle. Here the order of actuation is changed each 720° crank angle in order to achieve even wear of both spark plugs in a cylinder and to prevent one-sided accumulation of deposits in the combustion chamber.
Ion current measurement
Ions are created in the flame front during combustion (particles which have various different electrical charges) which balance each other out again in the burnt mixture. The application of a relatively small measuring voltage to the end of the spark plug allows one to measure this ion current through the flame. The measuring voltage is applied to the primary side of the ignition coils (auxiliary voltage of about 23 volts). This gives an AC voltage on the secondary side of about 1 kV with about 65 kHz on the spark plug electrodes.
The ion current modulates this voltage. Decoupling and filtering allows one to obtain an ion current signal. The ion current signal gives information about the rate of cylinder pressure with a degree of accuracy, which allows the detection of combustion misfiring.
The ion current signal is transferred to the control unit ME for every 3 cylinders. The cylinder concerned in each case is allocated in the control unit ME with the help of measuring windows. The chemical formula for the creation of ions in the flame is:

Ion current measurement at the spark plug delivers a signal directly from the combustion chamber without the use of any additional components such as combustion chamber pressure sensors.
The measurement is taken after ignition has been initiated by both spark plugs and a short waiting time. The measurement is only taken on the spark plug which first sparked. The distance between the electrodes does not have any effect on the ion current signal.
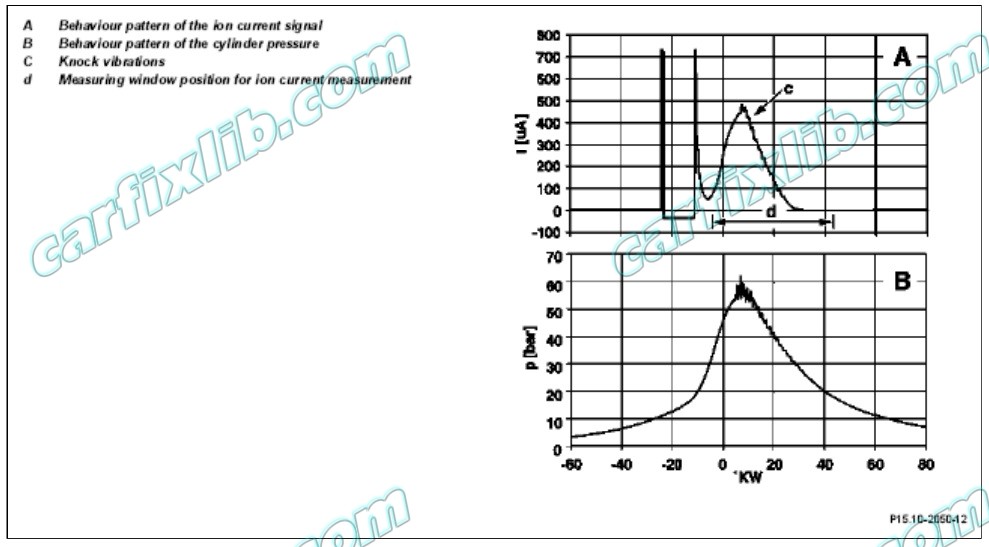
The profiles of the ion current signal and cylinder pressure are the same during combustion. Through this behavior, the evaluated ion current signal is used to detect combustion misfires reliably in all operating conditions and at all engine speeds. This is used for actuating the spark duration, for spark plugs diagnosis, for diagnosis according to OBD or EURO4 and for cylinderspecific fuel cut-off.
ECI Ignition System Power Pack Design

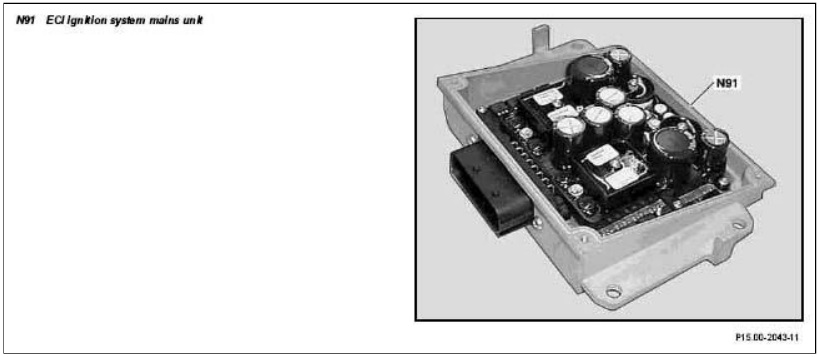
Electrical structure:
The DC converter is built discretely out of condensers, coils, transistors etc.. The DC voltages so generated have a load dependent duty cycle of about 10 to 90%, while the frequency is about 20 kHz (180 volts) and 65 kHz (23 volts).
The ECI ignition system power pack is fitted with an electronic overload protection for the voltages 180 volts and 23 volts. The outputs are switched off if a short-circuit or overload situation arises. They will remain locked out until the ignition is switched on again. Protection of the battery voltage which is looped to the ignition modules takes place on the vehicle side.
Mechanical structure:
An aluminum die cast housing with plastic cover.
The ignition must not be switched on without an earth connection to the power pack for the ignition system ECI is order to avoid any damage occurring. The earth connection is achieved over the housing.
Was this helpful?
1 / 0